Logistics
Greg Crimmins on January 19, 2017
As I am writing, I am waiting for the delivery of something that is both trivial and absolutely critical: 100 pieces of rectangular plastic, about 6 inches by 3 inches, with 96 little wells in them that can each hold about one third of a milliliter of liquid. These plates probably get stamped out by the hundreds of thousands, and I have used thousands of them in my career, yet my entire week-long experiment cannot move forward until they arrive.
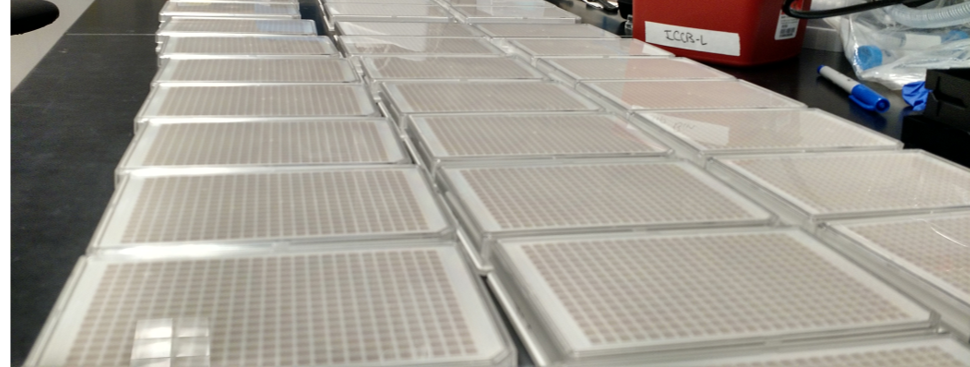
The delivery will hopefully be here in an hour or less, and while I wait, logistics is definitely on my mind.
When we rented the space that has since become the Remedy Plan lab, it was an empty room with empty cupboards and shelves. Prior to Remedy Plan, I would walk into a lab and everything I needed for my experiments was already there. The machines were functioning and calibrated (usually), the shelves were stocked with years worth of chemicals, piles of old glassware and tubes and beakers were stacked and ready for use, and the labs were filled with mountains of sterile, consumable plastic tools– like those 96-well plates I’m waiting on. There was a system in place to keep those labs continuously stocked and vendor agreements were often kept in place for decades.
Starting Remedy Plan meant starting with a blank slate. We had no vendors, no supplies, no negotiated prices… and we needed everything immediately to get our experiments off the ground. Over the last year, we have purchased supplies and equipment from at least 15 different companies. To stock the shelves, we’ve bought simple cleaning materials from the local Target and ordered highly-specified biological supplies from Thermo Fisher Scientific. On a daily basis, the cells we buy from one company are kept alive using media from a second company, serum from a third, and antibiotics from a fourth. These cells are grown in plastic flasks from a fifth company, in an incubator purchased from a sixth, which runs on a CO2 gas tank from a seventh. And when we run experiments on these cells, we use tens of thousands of pipette tips, hundreds of plastic plates, serological pipettes, scrapers, various flasks and tubes, gloves, multi-channel pipettes, reagents, de-ionized water, isopropyl alcohol, bleach, microscopes, water baths, an automated plate reader, computers, waste disposal bags… In short, a lot of supplies and logistics goes into each step.
Making sure we have everything we need just when we need it (especially since we don’t have excess storage facilities) can boggle the mind. If just one of those things is delayed in its delivery—like today—an experiment can come to a halt. Last month we had to delay an experiment for a day while we repaired our biosafety cabinet, a critical piece of equipment that had developed a faulty fan. Along with learning to run a company, we’ve also had to learn how to keep our lab running smoothly.
So as I wait here for those critical plastic plates I need to dilute the drugs I’m testing today, I have a newfound appreciation for logistics. Though, seriously, I hope they hurry up and get here before lunch. I have work to do.